fisha
Member Since: 25 Sep 2009
Location: Scotland
Posts: 1473

|
ACE pipe replacement / heater cross over pipes (no lift) | |
Now the job is done, I'll post up some thoughts / observations / tips / photos that can might help others if your trying this as a DIY job.
This isn't a full on how-to guide as many steps are missed. Its just comments on how I did it as a reference, so that it may help others who want to try the same, but may not have access to post lifts etc. ( There is no doubt a lift would have helped. Dont think I've done so many sit-ups from crawling about under the car ! )
Many thanks go to Pete (Haylands) and Mikey (plus anyone else whos posted about replacing ACE pipes on forums) for their help / thoughts and advice on doing the job, genuinely couldn't have done it without their prior knowledge / experience being offered.
Before tackling the job, have a read around some of the other threads such as:
https://www.fullfatrr.com/forum/topic67828.html
Note the prep of the new pipes - i did the same.
Tools I used / needed / found useful
2 basic trolley jacks - not workshop jacks with the handles attached, you need the jacks to be able to go under the car.
2 axle stands
Decent 6 sided socket sets.
Decent torx socket sets
Decent spanners
Bolt head extractors like these as some sill bolts were tight / stripped
Large subframe bolts - 18mm
Medium subframe bolts - 15mm
There was also 13mm bolts too ( like the collet holding the pipes into the valve block )
Pipe brackets, sill protections - typically 10mm
Pipe unions were 18mm and 20mm iirc.
Workarea: For the rear pipe, I needed about 2m of space to the LHS of the car to allow me to feed the pipe into the wheelarch area whilst the rest of the pipe stuck out to the left.
Initial prep steps:
Put it in off road height, and then remove the sill covers on both sides. ( take the end sections off, then the outer cover, then the inner cover.
Take the exhaust off from the mid-section backwards. It comes off easier if you undo all the hangers at the rear, and then support it with a jack to keep it level. You can hit it out by using a ball joint splitter fork inserted across the bracket joining the 2 pipes together just a couple of inches downstream of where you are disconnecting it.
Whilst its on the ground, undo / loosen / refit the subframe bolts. Far better to get these loose whilst its on the ground and you can put force into it without fear of it tipping. Clean the rust off with a wire brush, and tap the socket (18mm ) on initially to ensure it fits all the way home so you get the max grip possible on the bolt head.
Do this by hand using a breaker bar. Get it to break away a bit and then re-tighten slightly, loosen more, tighten slightly, repeat.( Think of a 2-steps forward, 1 step back approach ). The bolt will quick lose its tension / tightness and easily come out with a ratchet rather than breaker bar on the socket.
Getting it high enough off the ground
Put it in off road height, the disconnect the fuses in the rear fuse box by the battery. I took out the 4 that were labelled with the air suspension sign
There was a 60A, 15A, 10A and 5A on mine.
Next put the 2 trolley jacks under the rear suspension arms. My halfords jacks have a round platform which fits nicely into the circle moulding that the airbag mount pokes through. Then jack up the car by the arms, and place the axle stands under the sill jack points. Get it high enough that when you let down the jacks, the wheels are left hanging in the air with the suspension fully extended.
As an example, you can see the general setup here: Axle stand on the sill, trolley jack supporting the diff/subframe, and it also shows how the jack I used slotted into the underside of the suspension arm.
Once up in the air, wheels off and I disconnected the airbags. Did this by undoing the pipe into the bag, and letting it hiss slowly to let the air out.
Lowering the subframe
You can now lower the subframe and hang it on its mounting bolts.
Prep: remove the heatshields to expose the propshaft, and then undo the 2 bolts that hold the centre carrier to the body. This allows enough flex in the prop to lower the subframe.
Each corner of the subframe has 2 plates top and bottom ... you dont need the lower plates present to hang the subframe - the bolts are big enough:
To remove them, I wound out 4 corners and lowered the frame by about 1" all round. Then placed a jack in the middle that supported the diff.
Then for each bolt in turn, I completely removed it, took out the top and bottom plates, then put the bolt back in a few turns so that there was enough grip on the threads to hold the weight. The trolley jack on the diff can help support / raise / lower as needed. At the end of this, the subframe will be hanging on the bolts leaving ~75-80mm gap all round.
Now is a good time to clean up / prep the chassis.
Depending on your climate, expect corrosion of the chassis. The plates are steel, mounted directly against alu, which will only end in corrosion of the alu. Mine was there, but not fatal. For example, this was the worst of the corners:
In fact, it was so bad, that the white alu oxide had built up with so much pressure, that the flat plate was bent out of the shape at the edges.
Cleaned up by scraping/chipping off, buff down with sand paper, cleaned and etch primed:
Later Dinitrol'ed, but see Pete's thread for more on that.
Further lowering of the subframe.
You can drop the subframe on 1 side further to give you another couple of inches of room ( invaluable ).
With the trolley jack supporting the diff, undo the LHS bolts completely, then lower the jack down. This will drop the LHS of the subframe where the pipes go over.
The pipes removal.
Nothing special about this. Remove them. Undo the rubber mounting bolts ( if they haven't already sheared ). and disconnect each end and waggle out to remove. Mine cam out in a 1 go by coming forwards.
In hindsight, just chop the blooming thing into sections and remove the sections. You're replacing it, so who cares!
Fitting new pipes
Prep: I took off the bracket at the rear end where the flex hoses start. This allowed the pipes to move around more when fitting them in. Bracket can be added back in once the pipes are roughly in place. ( pink dot on image )
You will need new rubber mounts ( LR038632 )- just buy some - all 3 of mine were wasted - ebay was cheapest for me at the time, but they are rip-roaringly expensive for what they are. ( green dots )
Finally, fitting the pipe ... hoorah, at last. OK, I'll try and describe this as best I can:
With the pipes almost upside down to how they fit on the car, feed the flex pipes into the space from the rough angle as shown by the arrow:
IIRC, I led with the flex hoses, and the rest of the length of pipes were almost at 90° out to to the side of the car. Then as you manipulate the flex ends up and over, I twisted the pipe work clockwise and brought the front ends of the pipes over towards the line of the sills. Think of it a little like cork-screwing the pipework in.
No two ways around it, it was a faff as the front end of the pipe kept getting caught on junk in the garage ( hence my suggestion for cleare space ), and the flex hoses kept getting caught on stuff around the subframe.
but what about the axle stand ? You have to get the pipes from outside the axle stand to inside it. To do this, I used the spare trolley jack and a block of wood to temperarily support the car, remove the axle stand, put the pipe past, and then re-instate the axle stand. The temp support site I used was the flat chassis casting ( pink dot ) just inside of the sill jack point ( green dot ).
From there, its home run time ... pipes and mounts can all be connected up.
Putting it all back together
Pretty much a case of reversing the procedure.
Prep: Deal with the subframe support plates. Pete powder coated his and put silicon sheet between the plate the chassis. I cleaned mine up with a wire brush on a drill, primed, painted and dinitrol'ed mine, and also put the silicon sheet between the upper plate and chassis. I used the plate as a template to cut around.
*** Follow up edit: ***
Since driving the car after all this work, I've noticed a marked improvement to the car in terms of road noise / vibration within the cabin. It wasn't just a case of going back to how it used to be before the work, it was markedly better and quieter and smoother feeling. I've spoken with Pete, and he came to the same conclusion I did, that the silicon pads must be doing a good job of isolating vibration from the subframe travelling into the chassis.
So I cant recommend enough to add the pads between the subframe plates and the chassis when doing this work.
***
Re-fit the subframe with NEW bolts. Hand tightened with the ratchet and breaker bars. I was advised to no go as high torqued as per the workshop manual. I'll let you be the judge of it for yourself at that point.
To get it back on its feet, I reconnected the airlines to the airbags, re-fitted the fuses, fitted the wheels and put the 2 trolley jacks back under the arms and jacked up the arms enough that the wheels where off the ground again. Then started the car, selected off road height, and the bags reinflated, lifted up the rear end off the axle stands supporting the sills. Removed the axle stands, and then lowered the jacks down to let the wheels sit on the ground.
Re-Alignment
There is play in the subframe bolts and supports which means the it can be re-mounted at a different alignment to what it was before being dropped, the workshop manual mentions getting the alignment down after this sort of work.
I cant remember exactly, and didn't take pictures, but was conscious of this during refit. I think I was able to spot that bolts, bushes and plates weren't lining up to the same wear points on first attempt.
To adjust, I just loosened the subframe bolts and manipulated the subframe into its old alignment and then re-tightened.
In hindsight, might be worth making indelible marks on pieces before removal to show alignments.
The diff plug
When you're putting it all back together, now is a really really really good time to change the oil int he rear diff.
I tried to do this last year, and failed because I stripped the plug socket. Because you have the exhaust off doing all this work, you can get much better access to the fill plug. I took the opporunity to extract the plug, fit a new one, and refill. I suggest you do the same.
The pic below shows the plug finally released after much heat from a MAP gas torch and hammering.
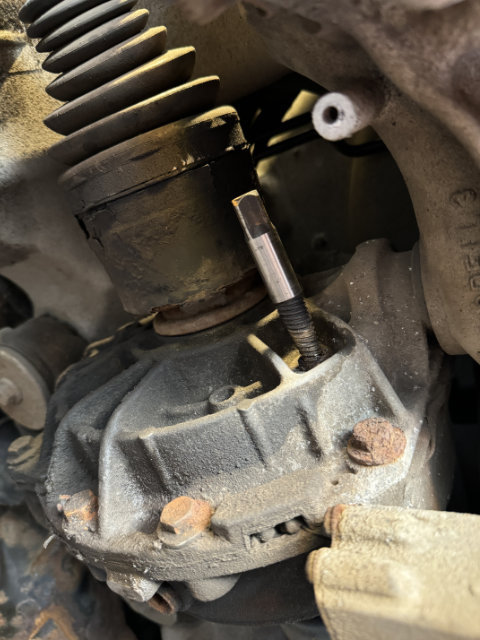 | Click image to enlarge | V8 or else ...
Last edited by fisha on 19th Sep 2024 4:35pm. Edited 9 times in total
|