First, a bit of background .....
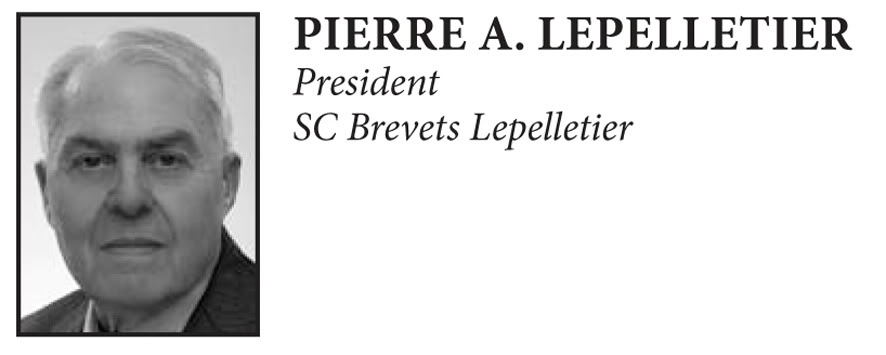 | Click image to enlarge |
Pierre Lepelletier is one of my heroes. He was born in 1928 and spent the whole of his career working for Ferodo (now Valeo) in France. At the age of 59 he took early retirement and then, two years later, filed a patent application for a new geartrain arrangement for automatic transmissions that could produce six well-spaced ratios using only 5 clutches, a Ravigneaux epicyclic and a simple epicyclic.
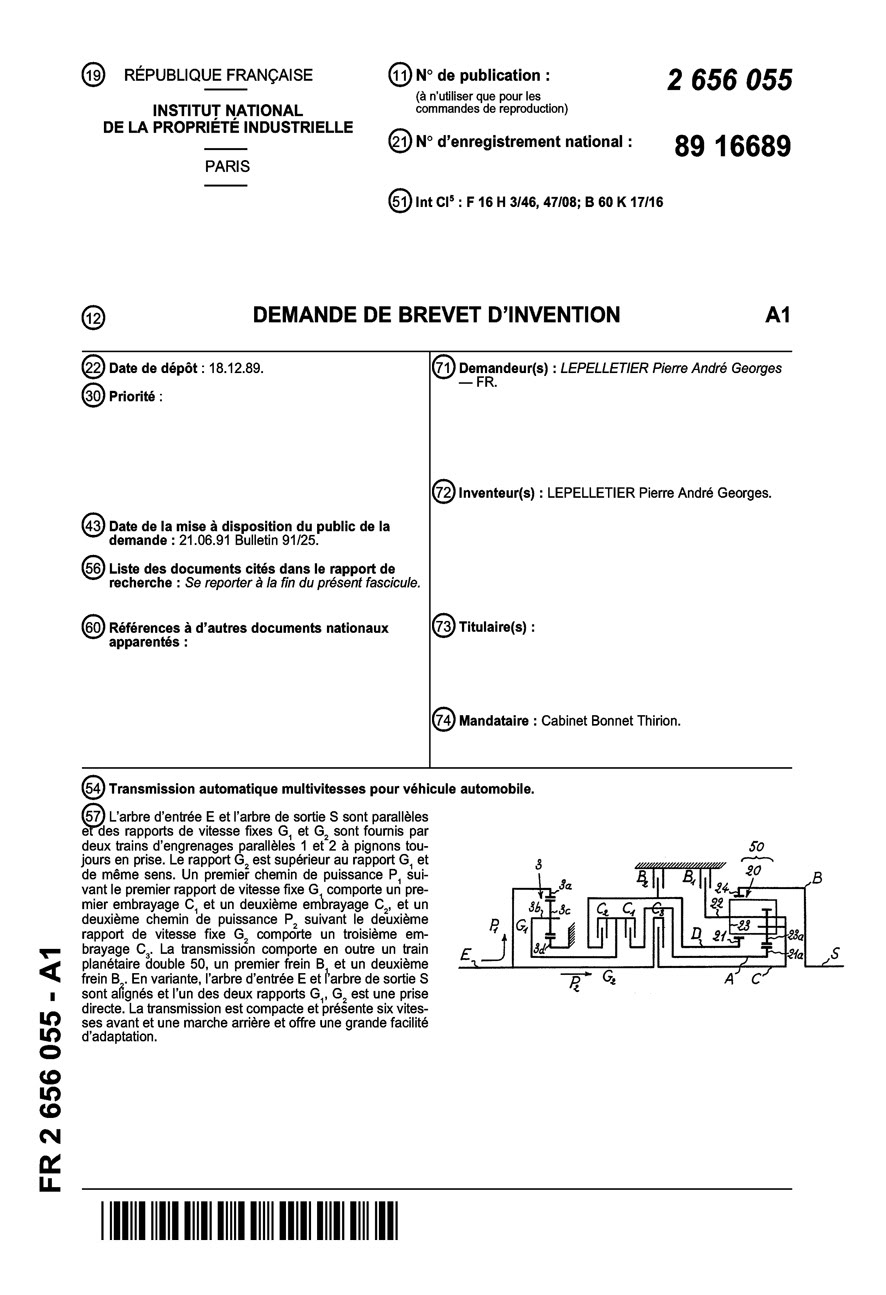 | Click image to enlarge |
This was in December 1989. A few years later he had signed licenses with Aisin-AW (the world’s largest automatic transmission manufacturer), ZF, Ford, Jatco & GM allowing them all to manufacture transmissions using his geartrain system.
Why was his invention so important? Well, in ZF’s case - compared with the 5-speed 5HP24 unit that it replaced - the 6HP26 had 29% fewer parts (down from 666 to 470), was 44mm shorter (reduced from 697mm to 653mm) and weighed 12% less, despite its higher torque capacity and increased ratio spread. Most of the world’s OEMs switched to 6-speed transmissions as a result.
A colleague of mine was lucky enough to meet and have a chat with Monsieur Lepelletier at a conference a few years ago and told me that he’s a perfect gentleman. Now in his mid-eighties, I hope he enjoys a long and healthy retirement – and hopefully he’s made a few quid from the 20 million or so 6-speed transmissions that have so far been produced using his patented design!
The ZF 6HP26 transmission first appeared in 2001 in the 7 Series BMW, the year before the L322 Range Rover was launched, but since Ford had taken Land Rover off BMW’s hands in 2000, the L322 driveline development was frozen resulting in the Range Rover being launched with the already out-of-date 5-speed ZF unit in 2002. It wasn’t until 2006MY, when the Jaguar petrol engines were introduced, that the Range Rover finally caught up and the 6-speed unit became available. The diesel version had to wait yet another year for the TDV8 to be introduced before the infamous GM 5L40-E was finally abandoned in favour of the 6HP26.
Strictly, the Range Rover is fitted with the ZF 6HP26X transmission (the ‘X’ stands for external 4WD i.e. fitted with a separate transfer box) with part numbers starting 1068 020 XXX, the rear-wheel drive variant being the ZF 6HP26 (part numbers starting 1068 010 XXX) and the ‘internal 4WD’ version for Audi & Bentley being designated the ZF 6HP26A61 with part numbers starting 1068 030 XXX.
Anyway, on with the teardown ….
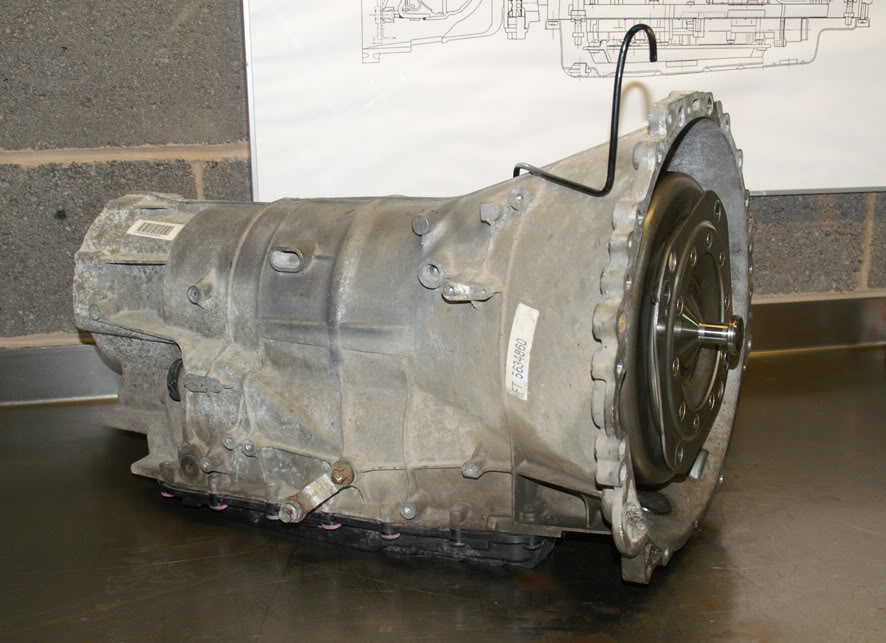 | Click image to enlarge |
I saw this particular transmission on eBay, actually from a supercharged 4.2l V8 Range Rover Sport, with a starting price of £50 – and I turned out to be the only bidder.
After sliding the torque converter off its splines, and placing it safely to one side, I drained out the transmission fluid. The drain plug is at the back of the plastic sump pan.
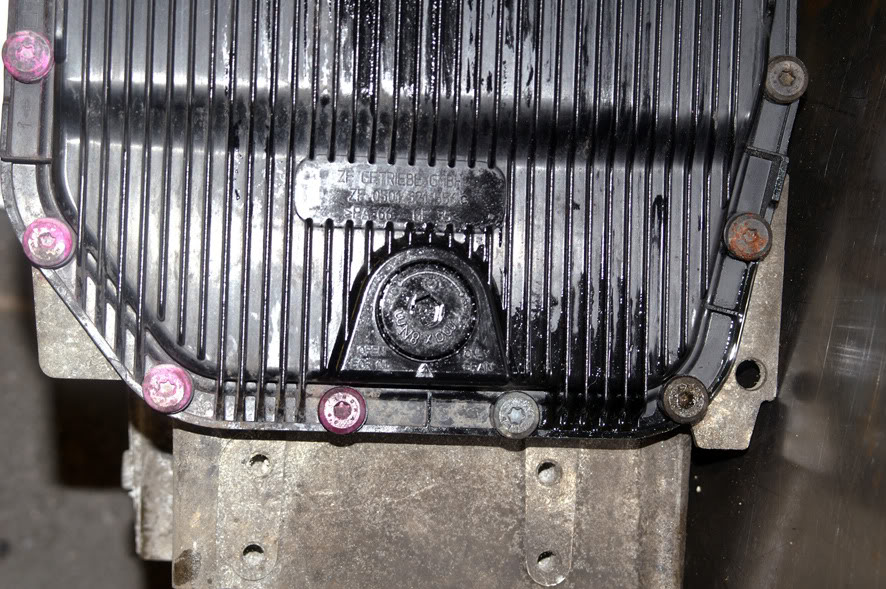 | Click image to enlarge |
Incidentally, the filler/level plug is on the right side of the casing, in a location similar to the 5-speed units
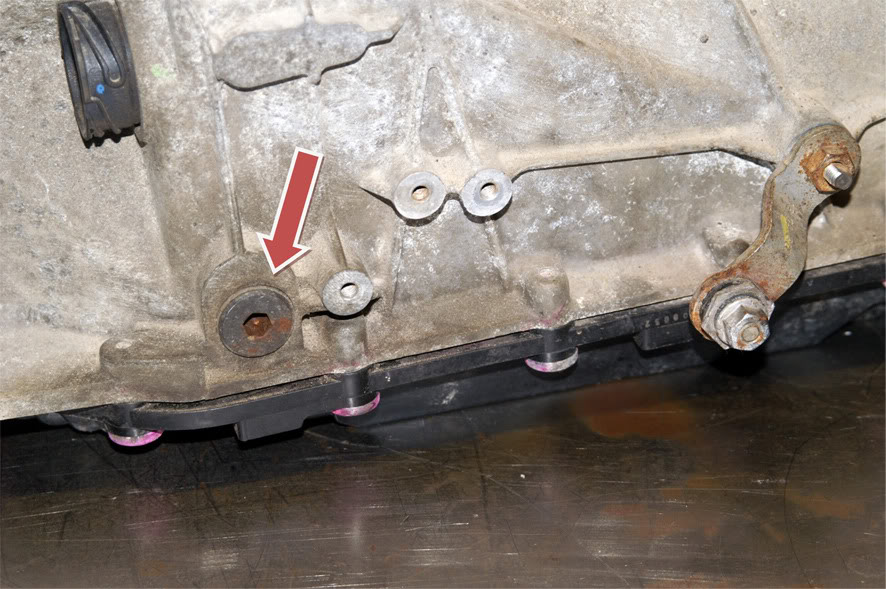 | Click image to enlarge |
Sump pan removal next – there are 21 screws in all and it’s good to see that the head size has been increased to Torx T40, from T27 used on the 5HP24, to make the heads less likely to strip
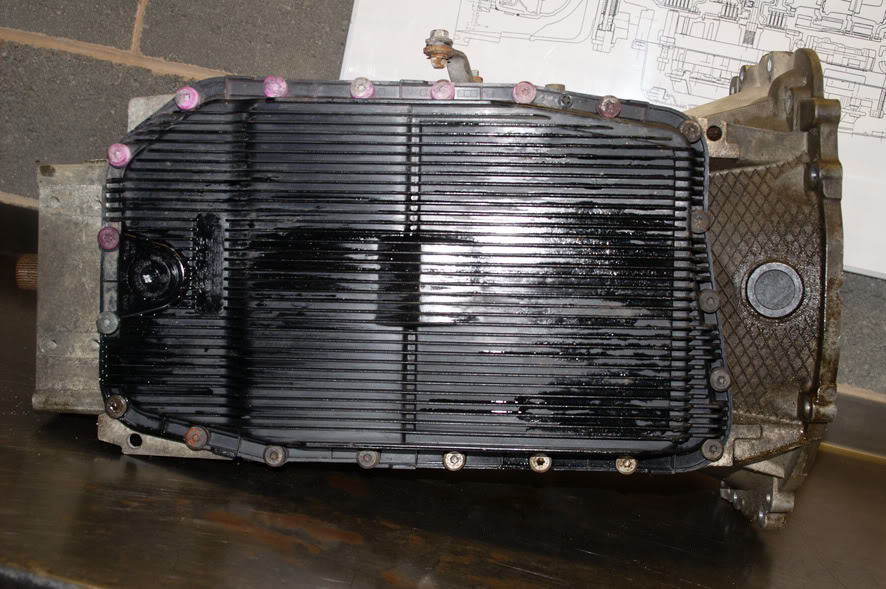 | Click image to enlarge |
These screws are tightened to 8Nm. ZF warn against removing the sump pan at fluid temperatures above 40 deg. C due to the risk of the plastic distorting at higher temperatures!
The sump pan then just pulls off
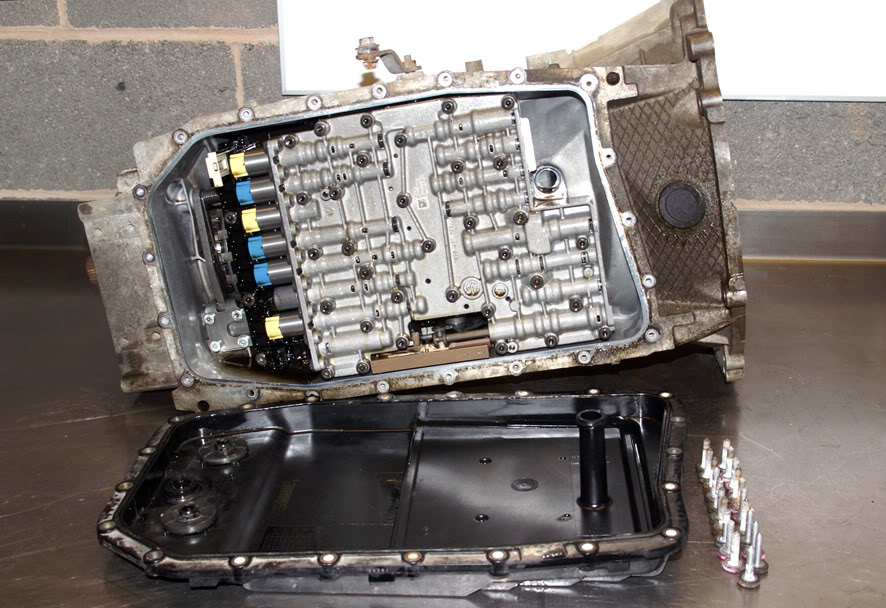 | Click image to enlarge |
The filter is an integral part of the sump pan and the photo shows where the oil enters the filter at the very bottom of the sump and also the suction tube which engages in a hole in the oil pump housing
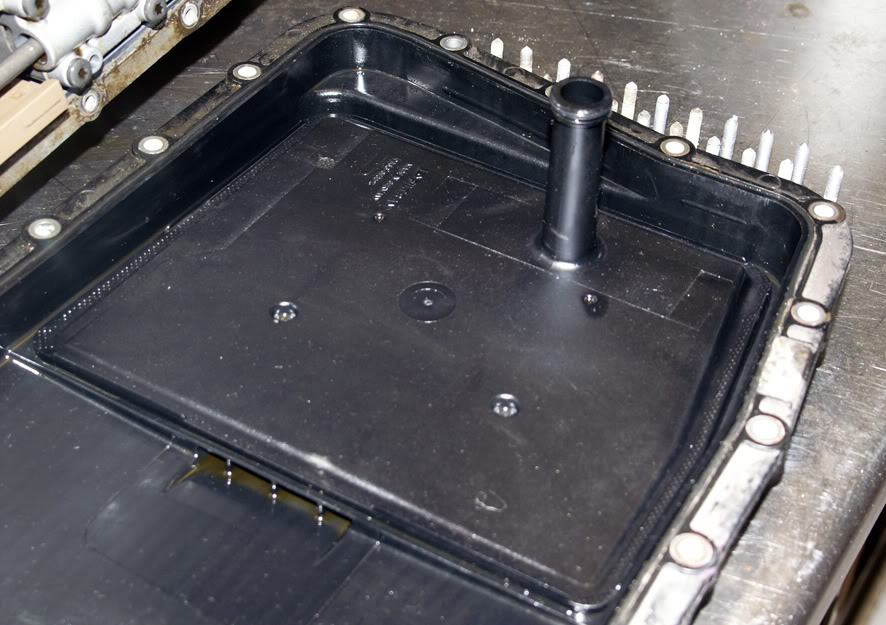 | Click image to enlarge |
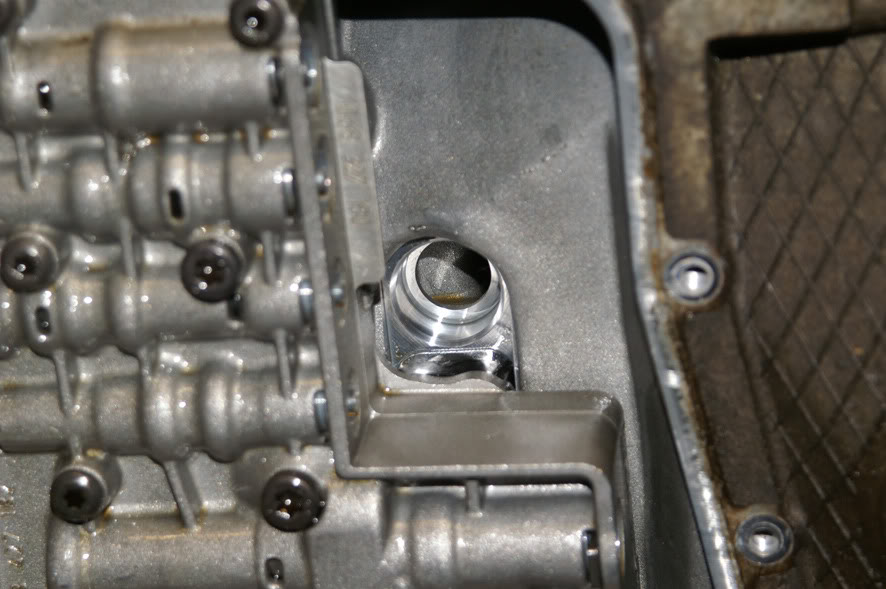 | Click image to enlarge |
This particular sump pan/filter had never been changed, as revealed by the 2005 date stamp
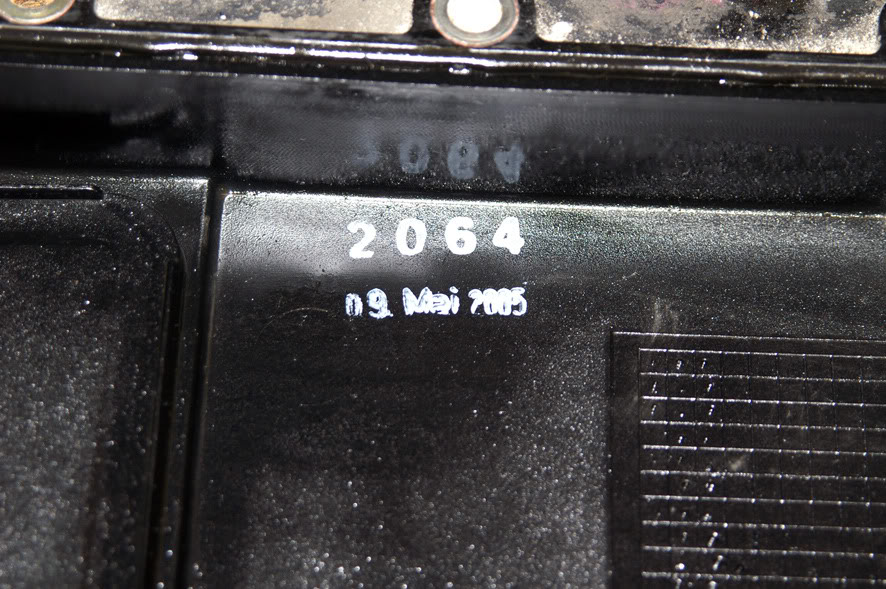 | Click image to enlarge |
The OEM is Filtran (as for the 5HP24)
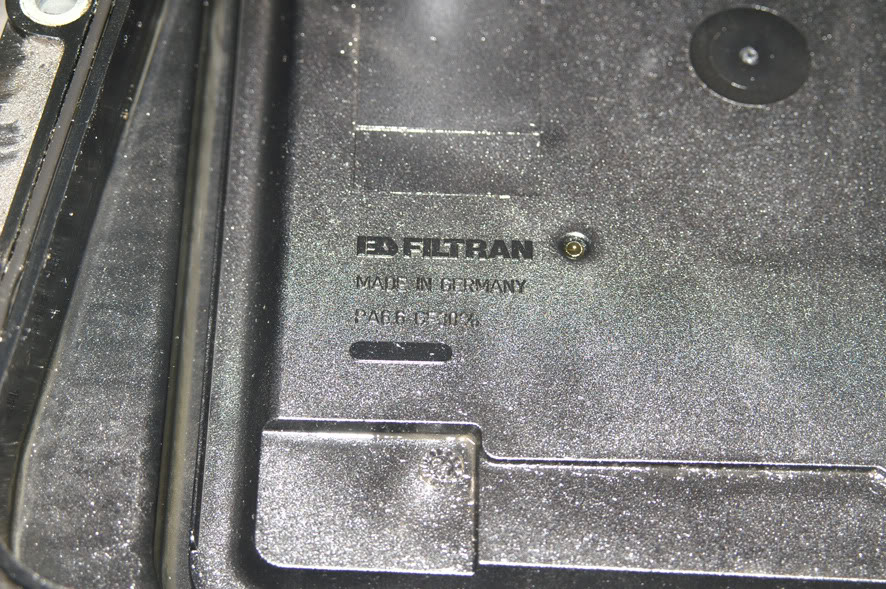 | Click image to enlarge |
and two sump magnets sit either side of the drain plug at the rear of the sump pan
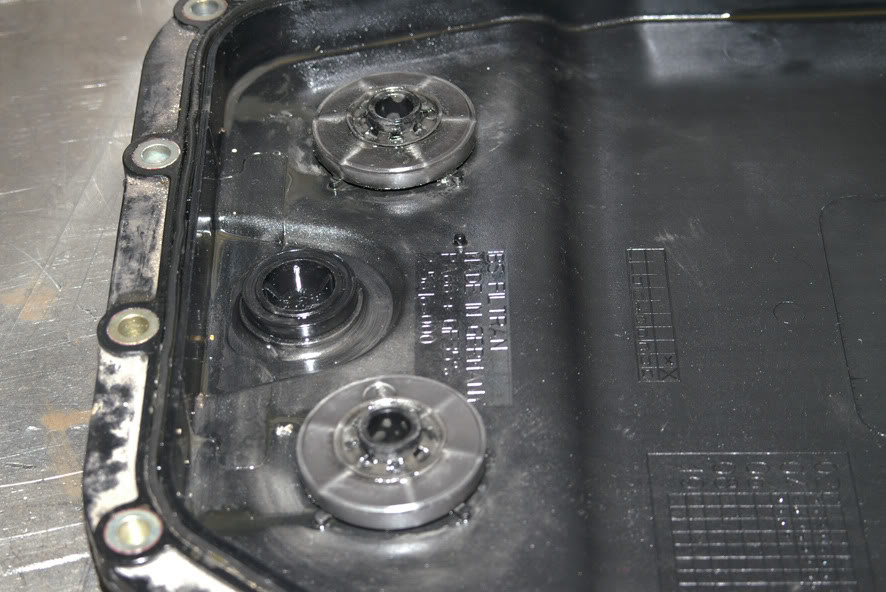 | Click image to enlarge |
The electrical connector sleeve is removed next, by first pulling out its retaining clip
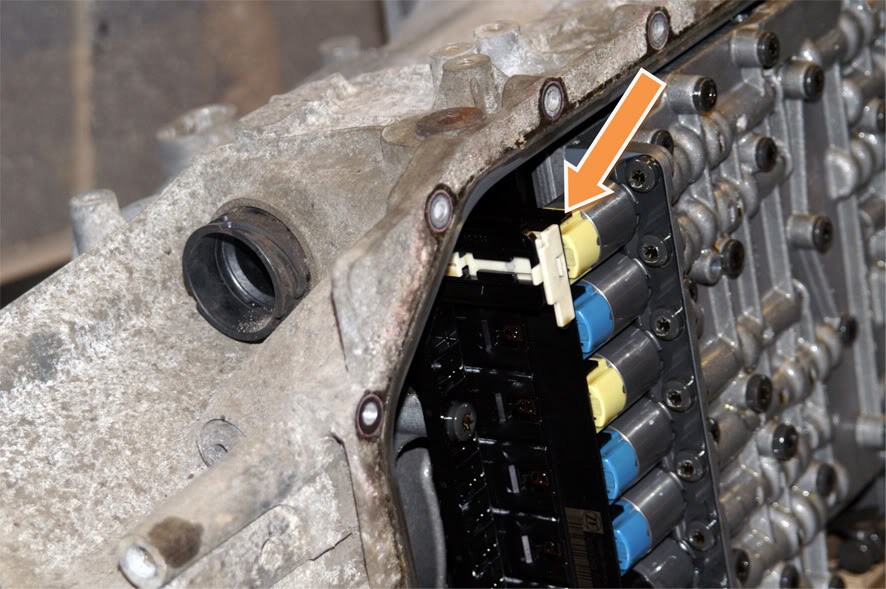 | Click image to enlarge |
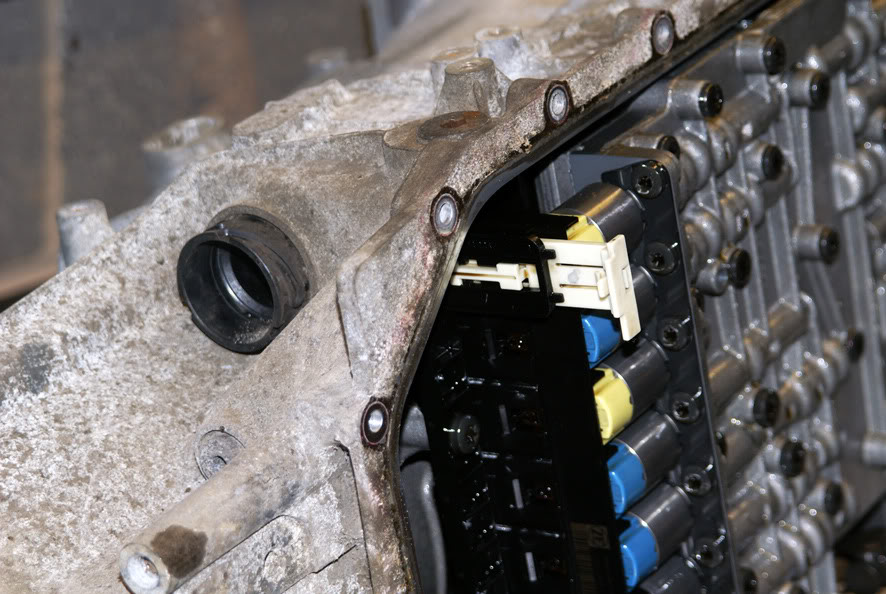 | Click image to enlarge |
and the connector sleeve will then come out of the casing
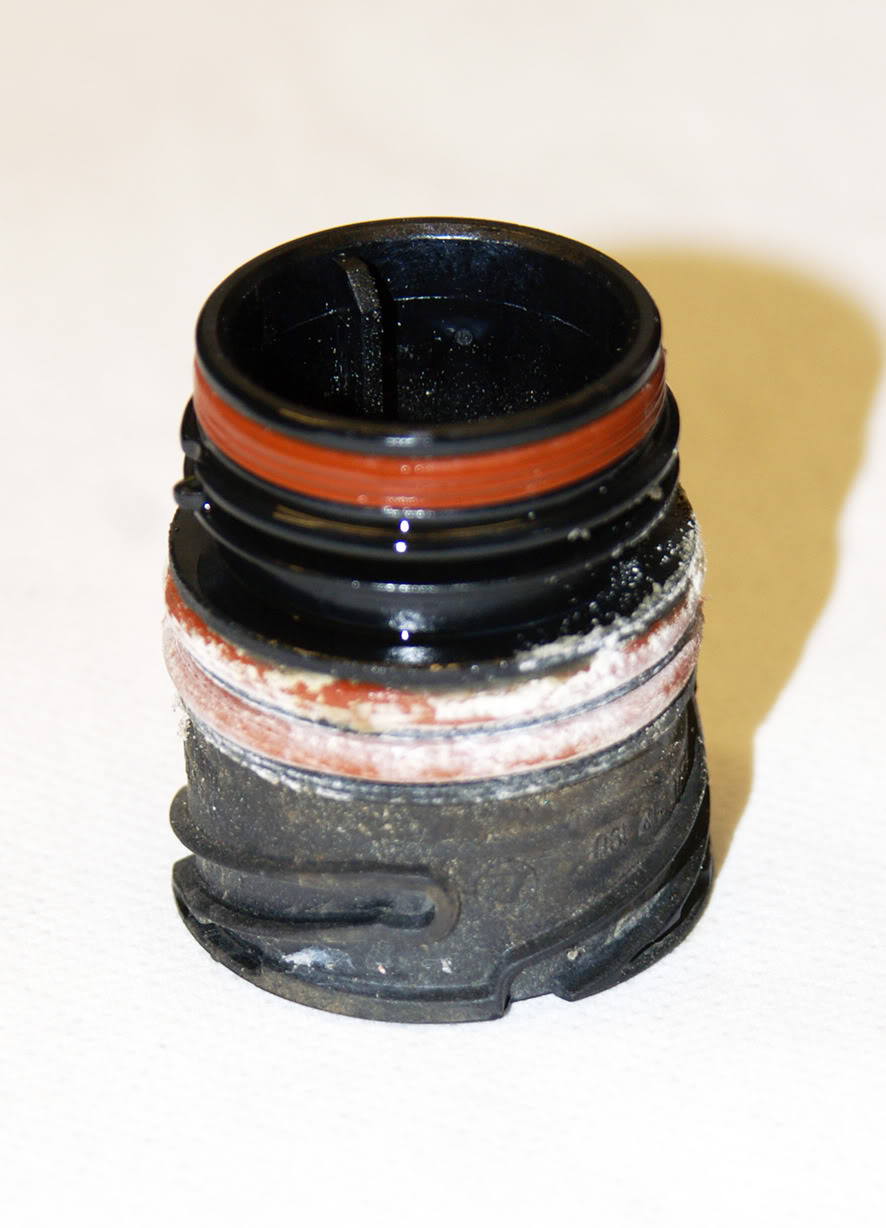 | Click image to enlarge |
It’s easy to see, from the casing corrosion which has coated the two O-ring seals, why this is a very common source of oil leaks in the 6HP26 transmission.
The electrical pins on the Mechatronic module can be seen through the hole in the casing where the sleeve was extracted
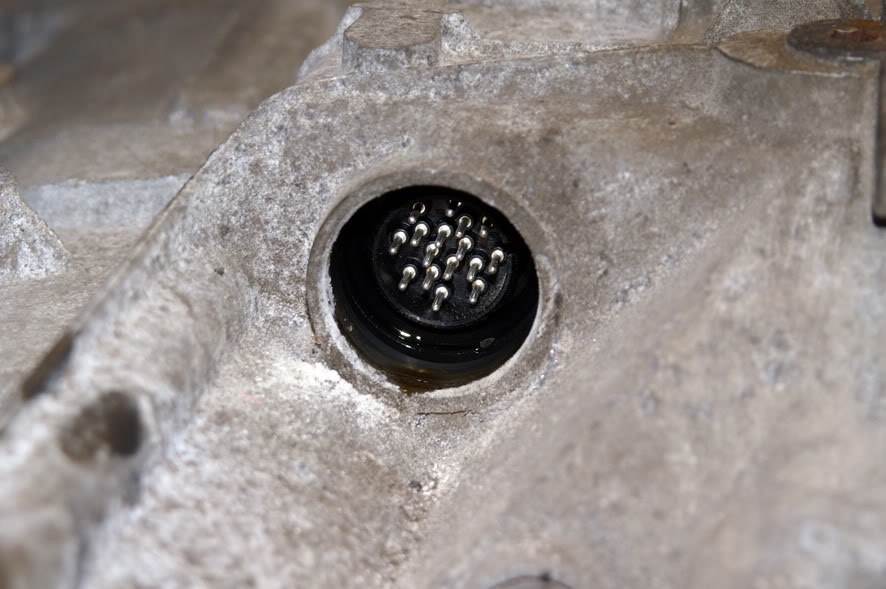 | Click image to enlarge |
There are ten screws in all (Torx T40) which bolt the Mechatronic module to the casing - seven long and three short - and these are easy to distinguish from the screws which hold the two valve block halves together which are only T27 and have a smaller head size
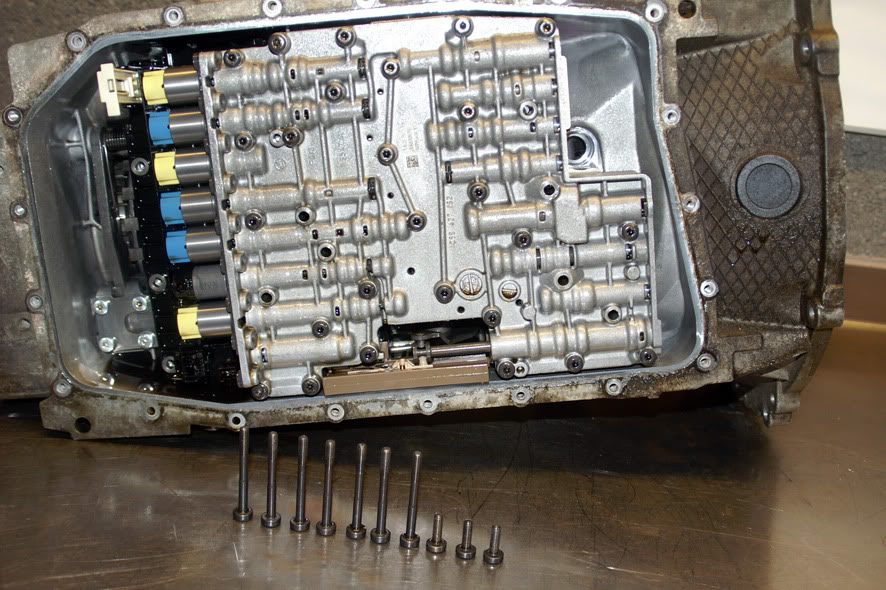 | Click image to enlarge |
The rooster comb pin engages in a slot in the manual valve which also drives the slider on the (brown) potentiometer so that the controller knows which gear position has been selected by the driver
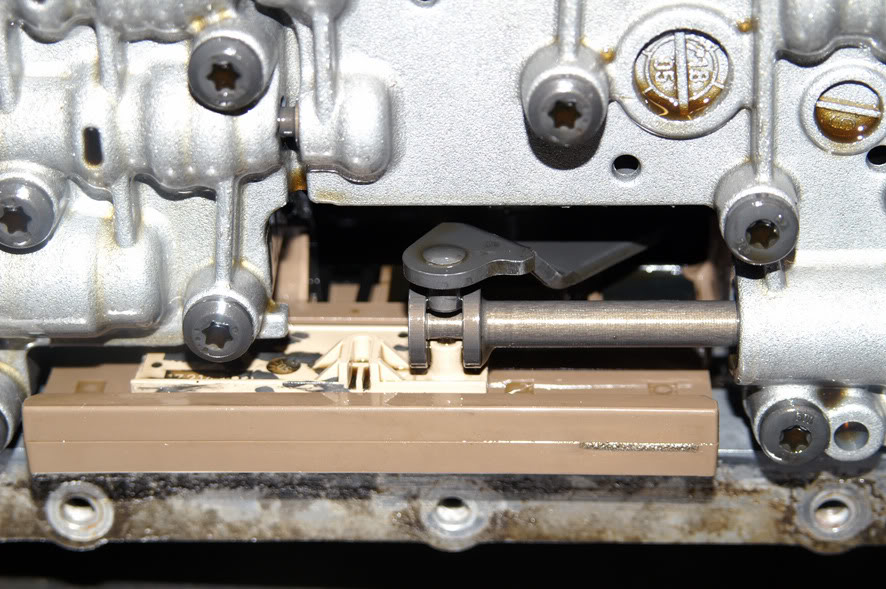 | Click image to enlarge |
The Mechatronic module can then be lifted out
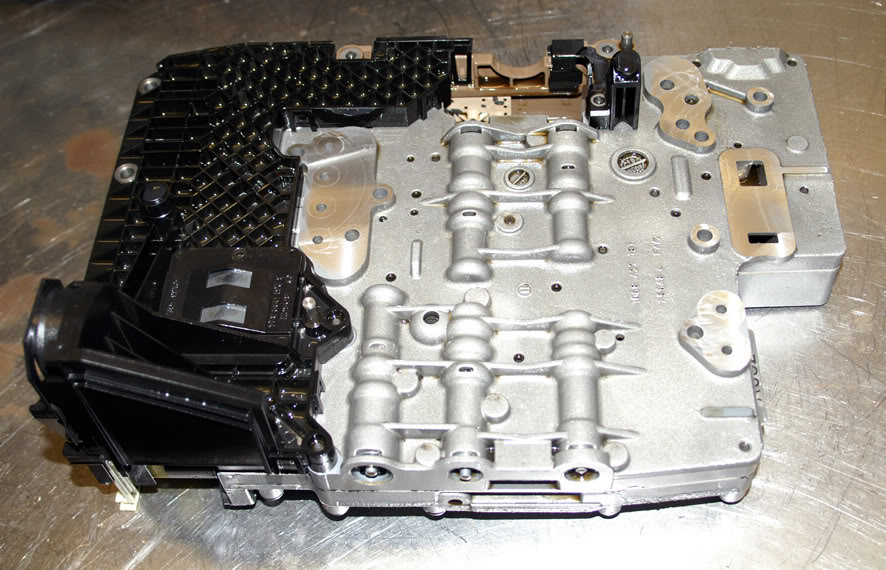 | Click image to enlarge |
The Mechatronic module is a combined hydraulic valve block and transmission ECU. It also houses both the turbine and output speed sensors and also the fluid temperature sensor. There’s a risk that electro-static discharge could damage the ECU so ZF recommend that a ground strap is worn when handling it
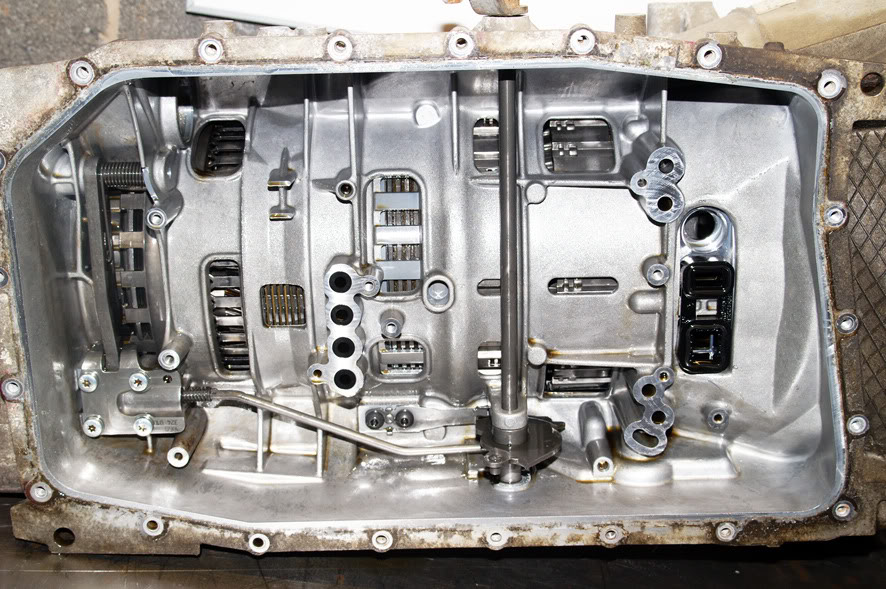 | Click image to enlarge |
This is how the underside of the casing looks with the Mechatronic module removed
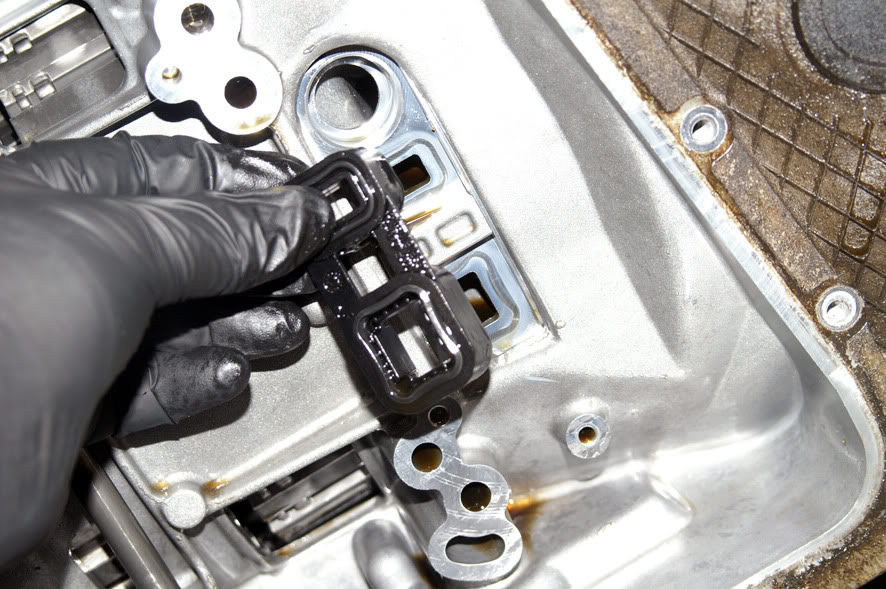 | Click image to enlarge |
Next, the bridge seal to the pump housing just lifts off
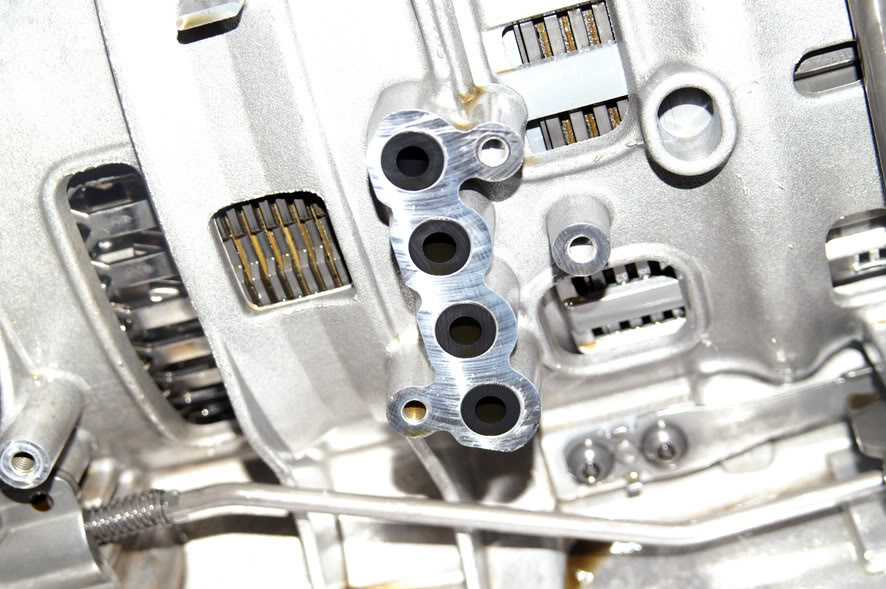 | Click image to enlarge |
and then each of the four rubber jump tubes has to be extracted
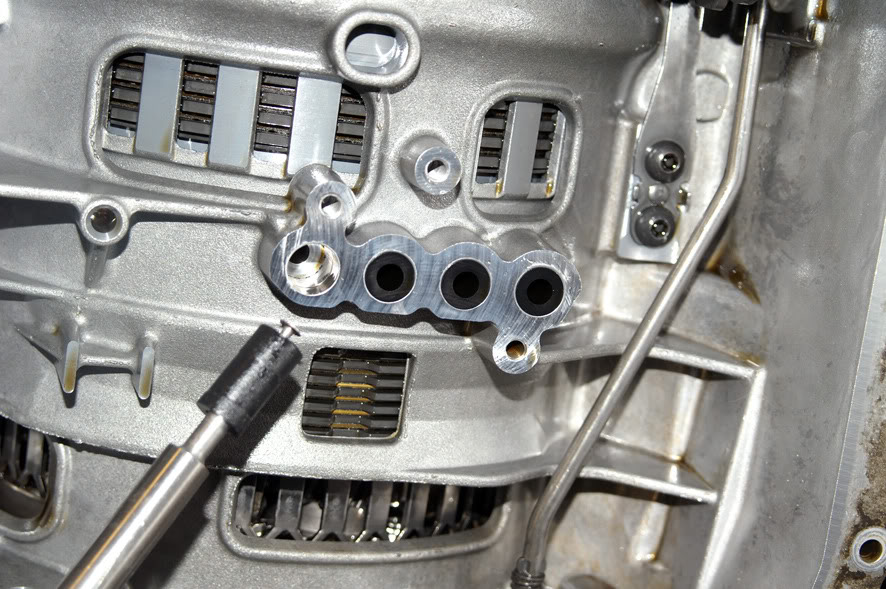 | Click image to enlarge |
In terms of length, there are two small, one medium and one large tube
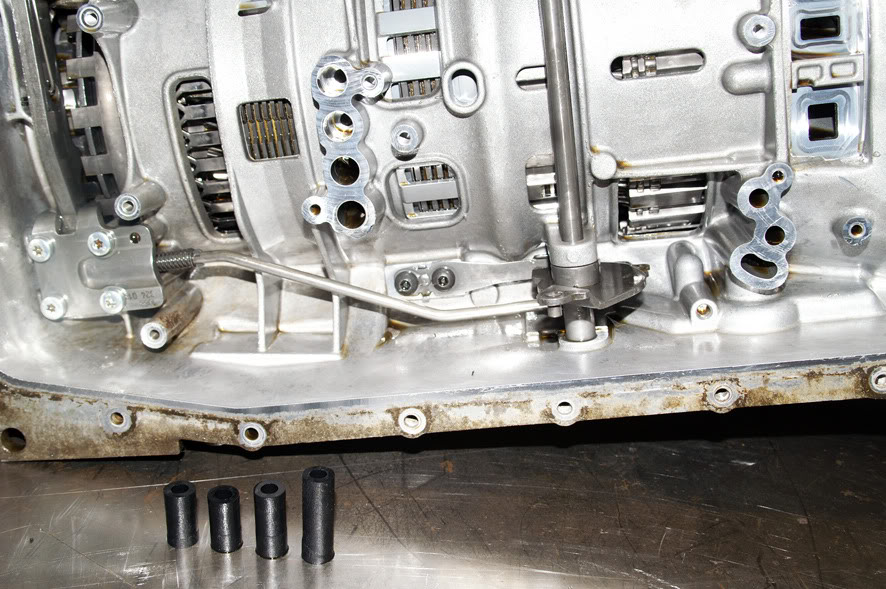 | Click image to enlarge |
The park lock engagement mechanism can be seen in the photo above and this is removed next, together with the selector shaft
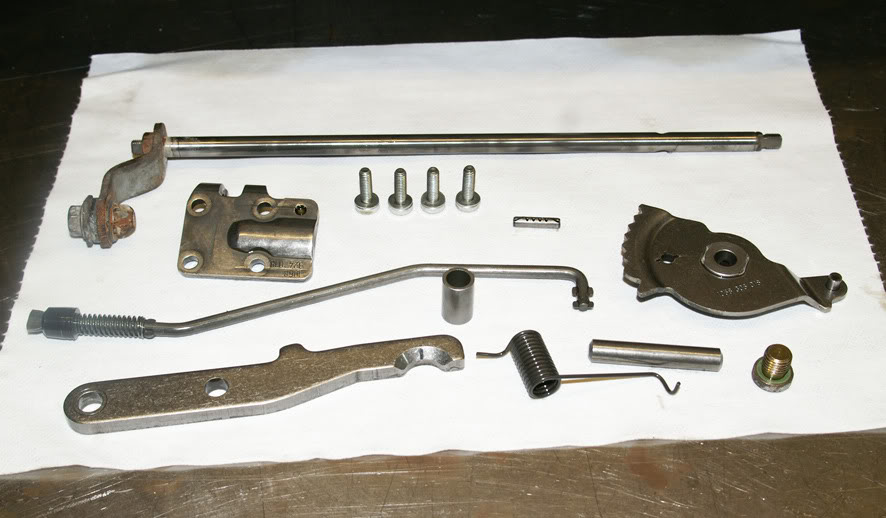 | Click image to enlarge |
So that’s it for the underside, next our attention turns to the front of the transmission.
The oil pump and stator support assembly is retained by 13 Torx T27 screws
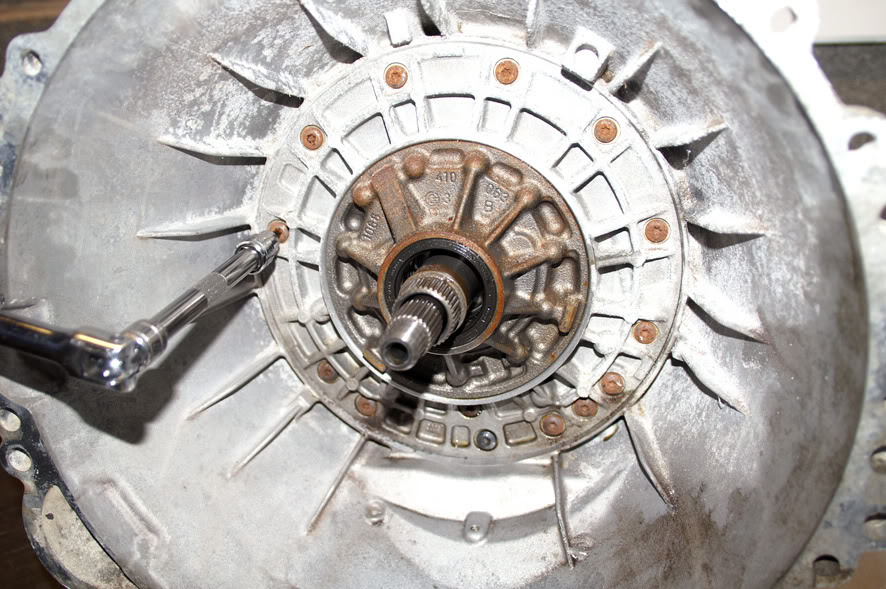 | Click image to enlarge |
and each of the (identical) screws is fitted with a washer with a rubber insert to prevent leaks
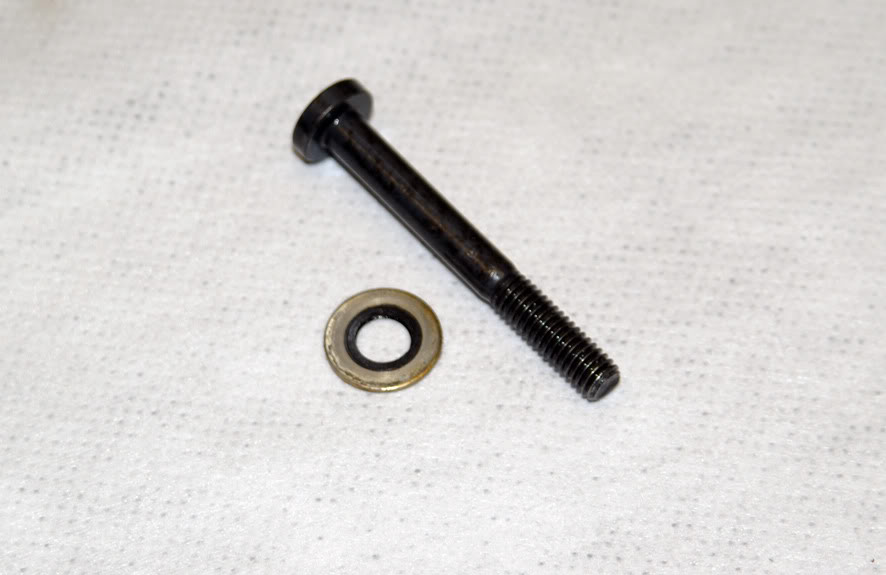 | Click image to enlarge |
The assembly can then be drawn out from the casing
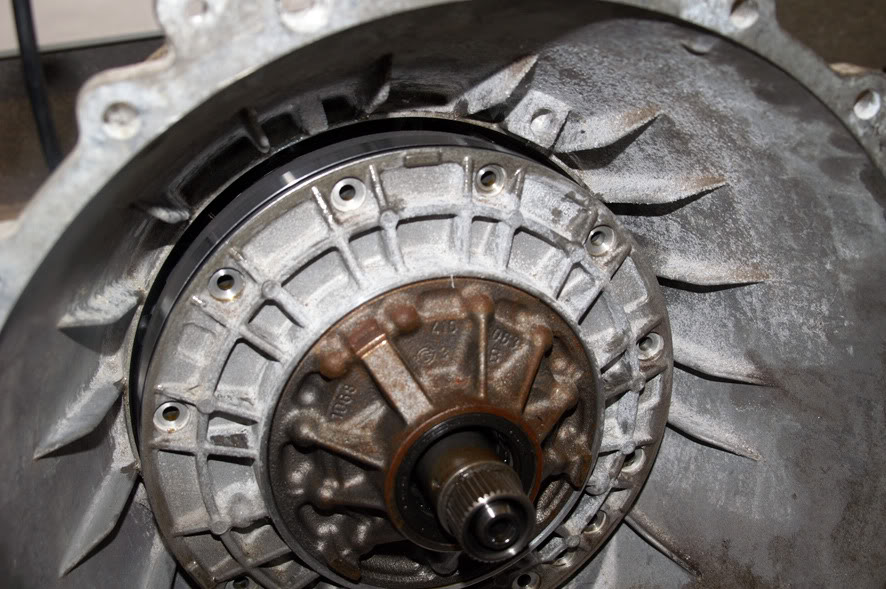 | Click image to enlarge |
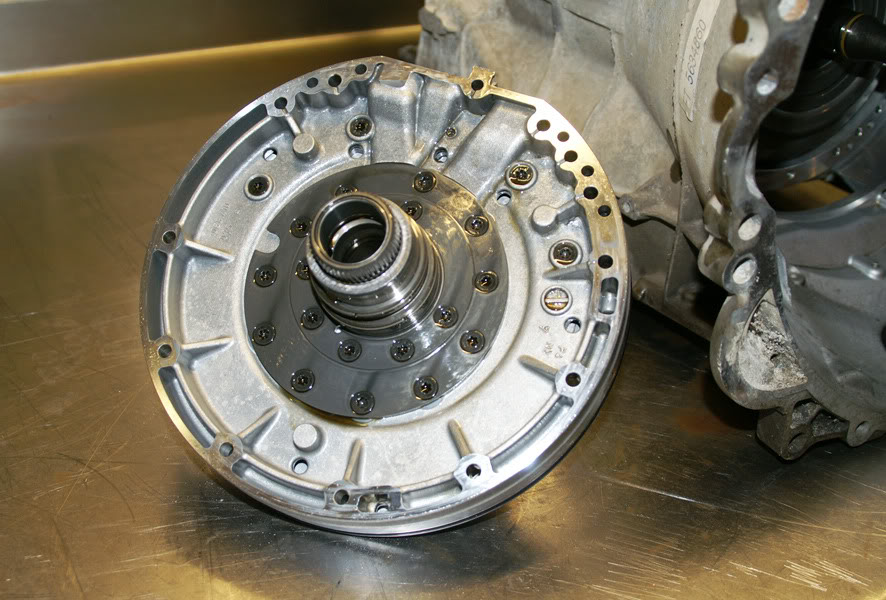 | Click image to enlarge |
Next out is the A & E clutch assembly, which includes the front epicyclic
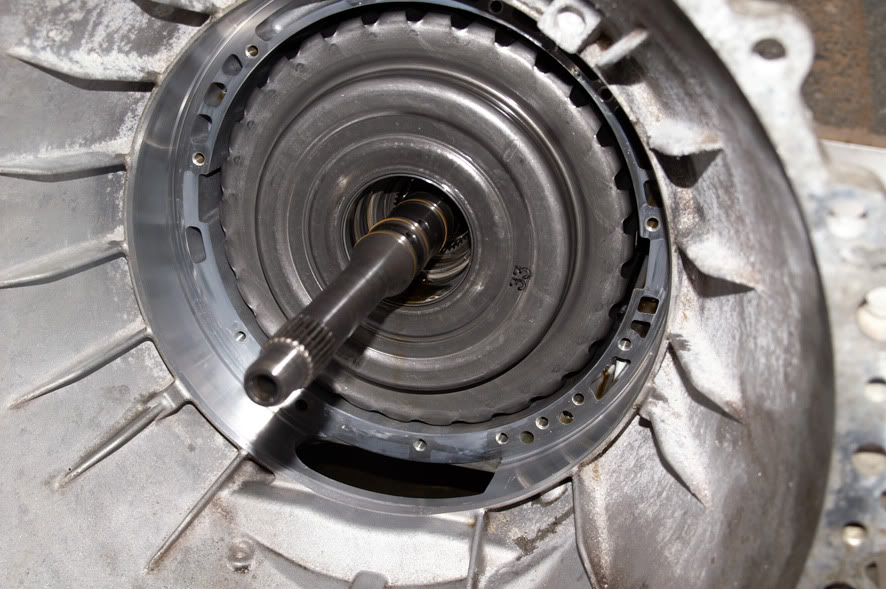 | Click image to enlarge |
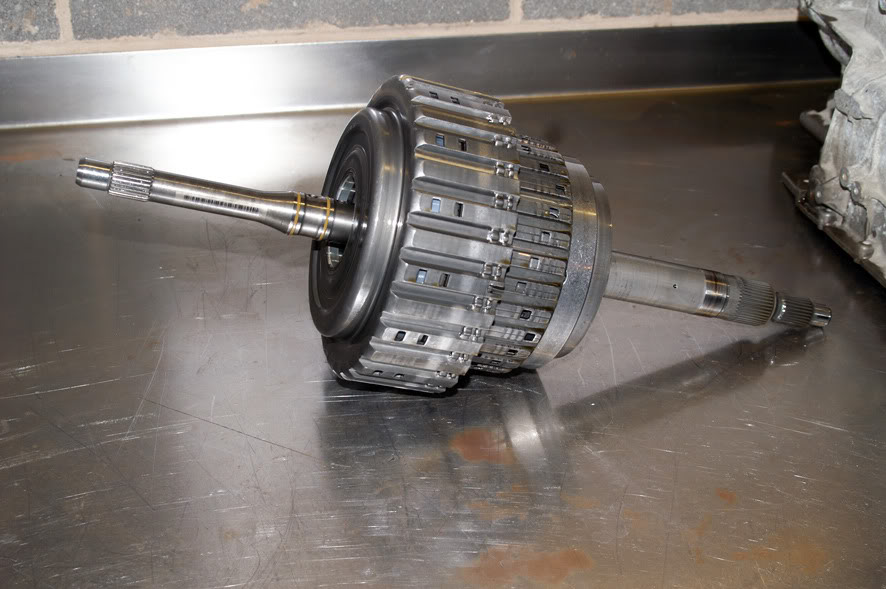 | Click image to enlarge |
Followed by the B clutch assembly
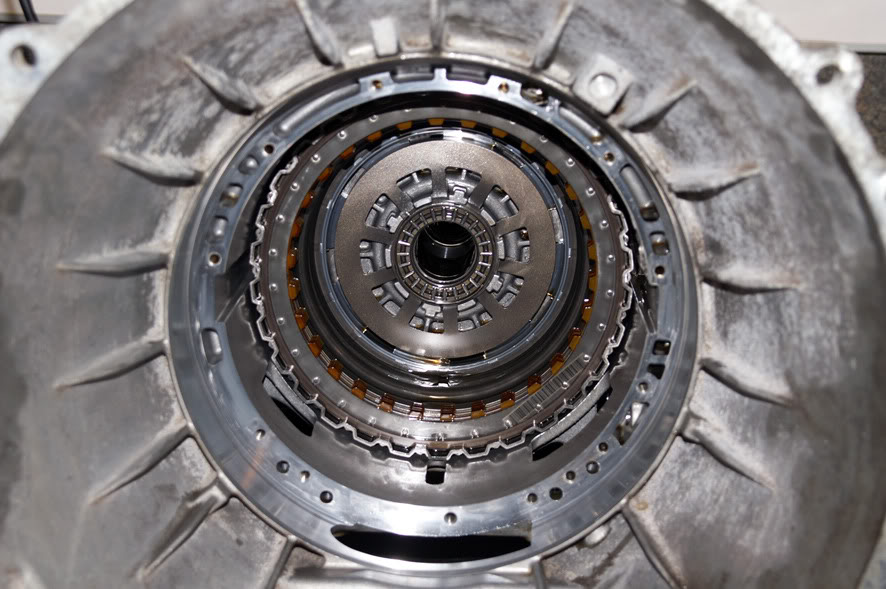 | Click image to enlarge |
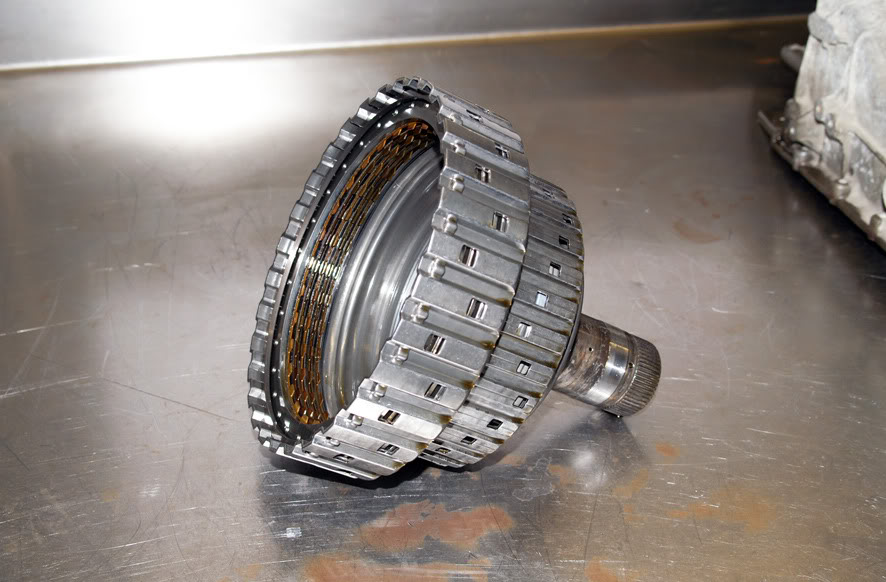 | Click image to enlarge |
To remove the static C clutch (& D clutch) housing, the large snap ring has to be extracted first
 | Click image to enlarge |
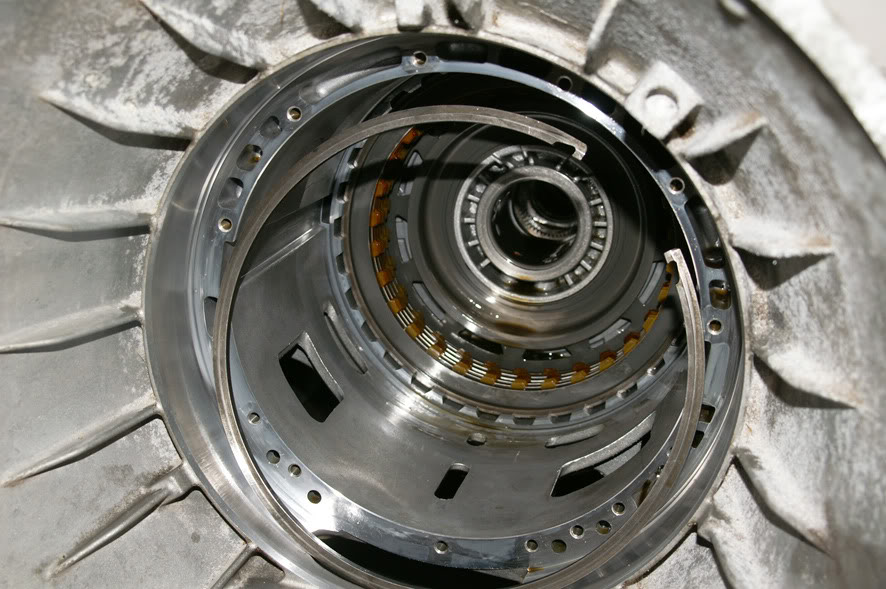 | Click image to enlarge |
and it can then be drawn out
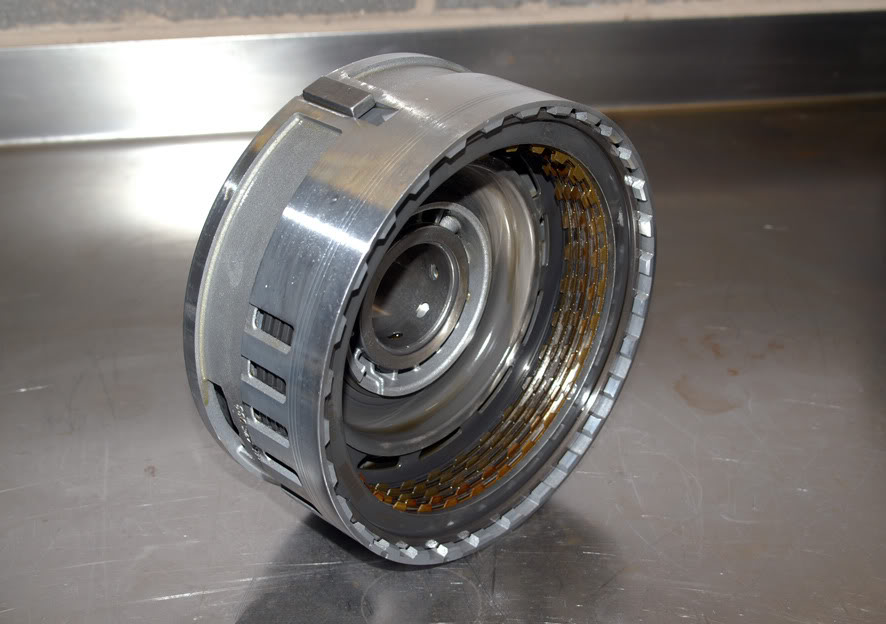 | Click image to enlarge |
The two rectangular blocks in slots on the outside of the drum prevent the assembly rotating in the casing
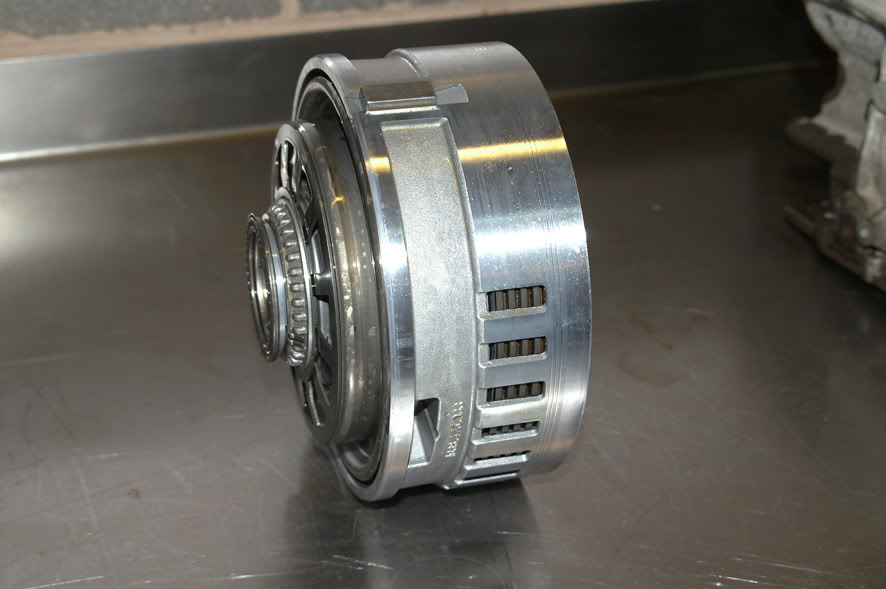 | Click image to enlarge |
Now the Ravigneaux epicyclic, together with the D clutch pack, follow
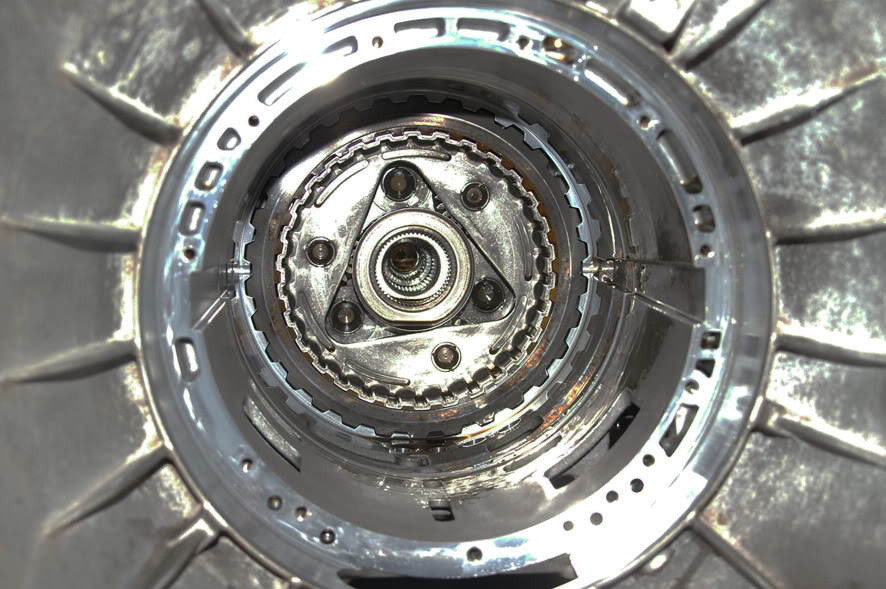 | Click image to enlarge |
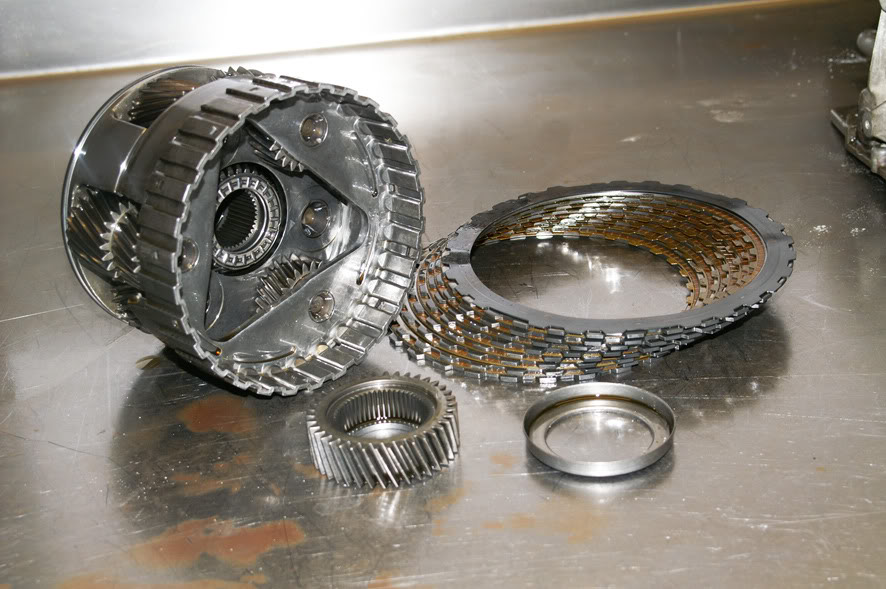 | Click image to enlarge |
Which just leaves the output shaft
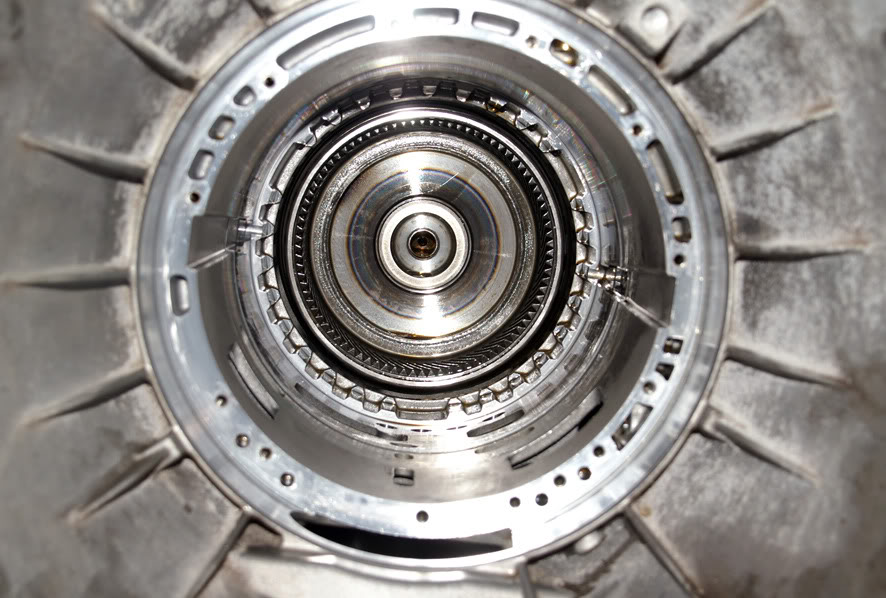 | Click image to enlarge |
The intricate basket weaving around the annulus gear is actually the target wheel for the output speed sensor
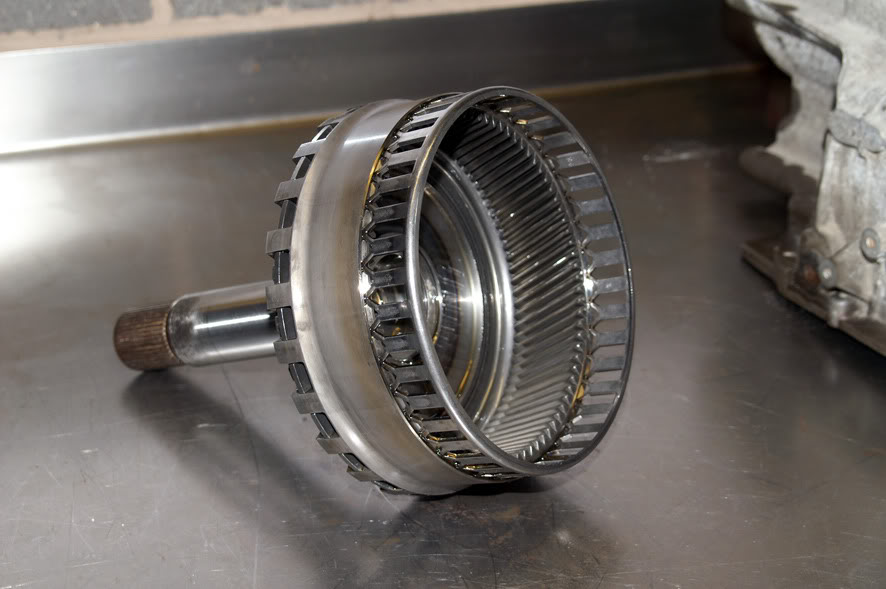 | Click image to enlarge |
Turning to the back of the transmission, the rear output seal is removed
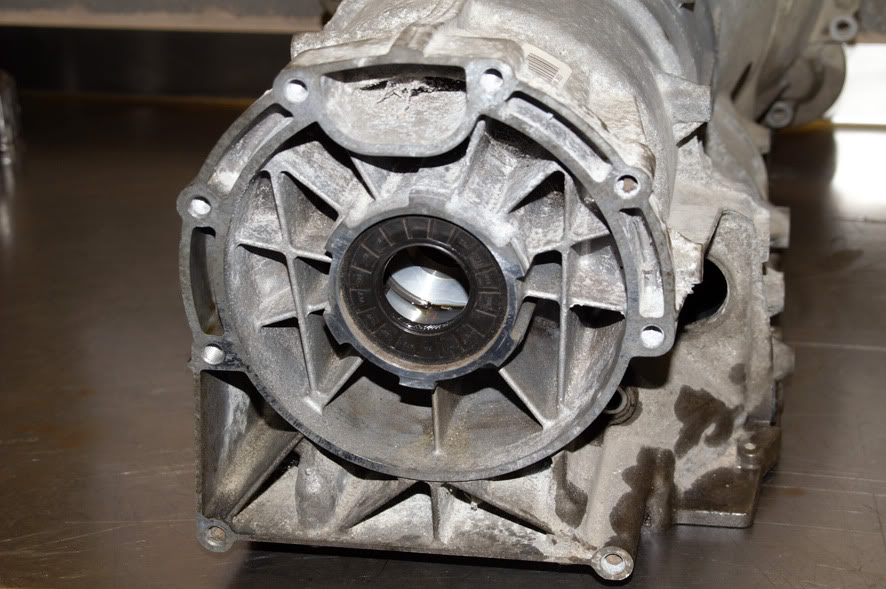 | Click image to enlarge |
to reveal a snap ring that retains the insert which locates the rear axial bearing
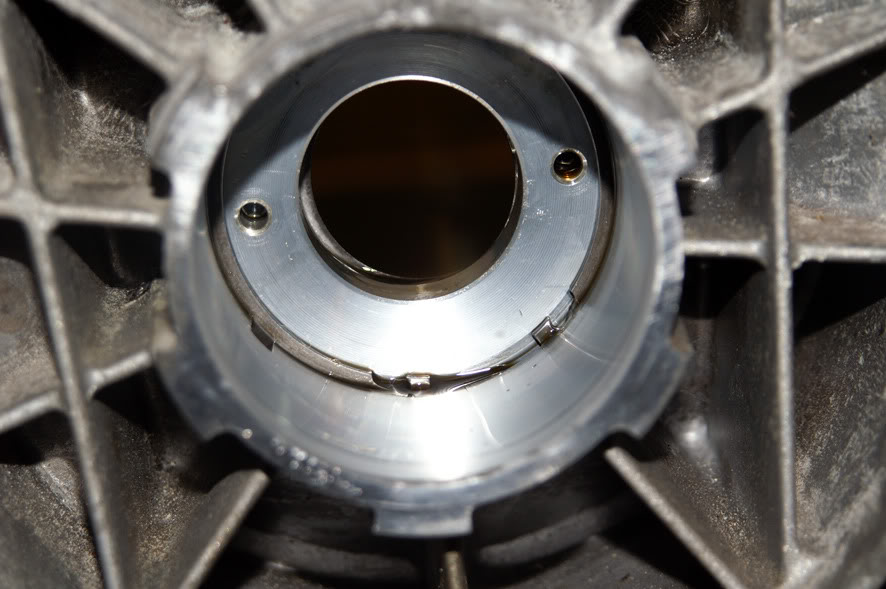 | Click image to enlarge |
A couple of threaded holes allow extraction bolts to be screwed in to assist with its removal
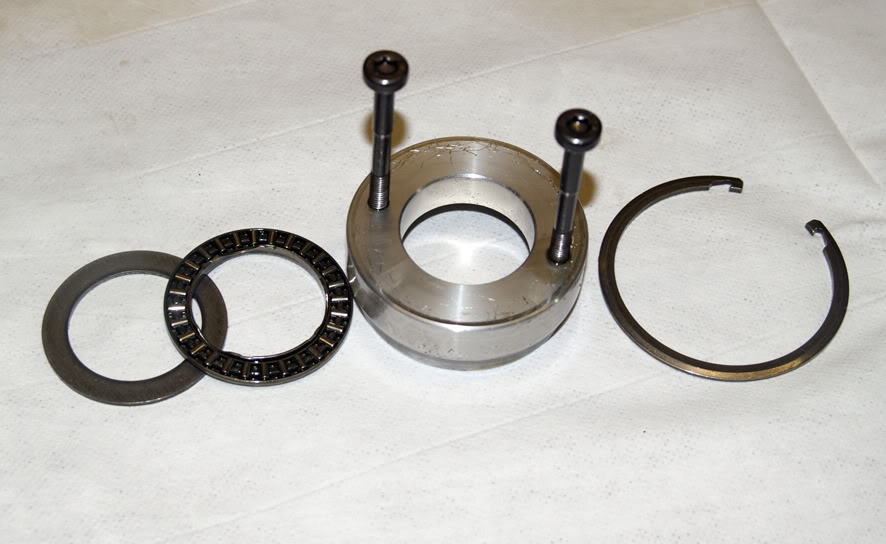 | Click image to enlarge |
So that’s just about it. The casing is now empty
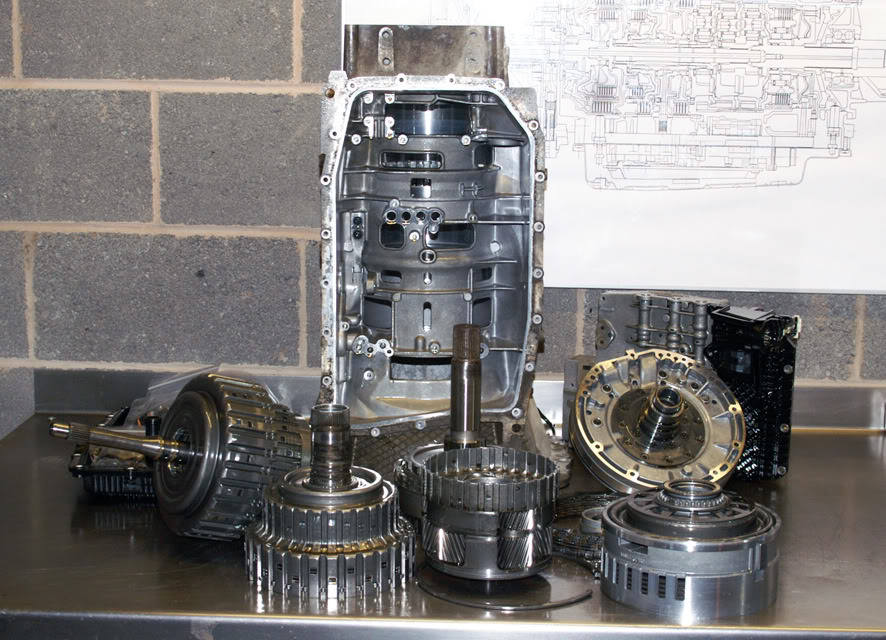 | Click image to enlarge |
A very simple process requiring no special tools.
Next step is to disassemble each of the subassemblies in turn. I’ll follow up with reports on progress with those.
Phil
Admin note: this post has had its images recovered from a money grabbing photo hosting site and reinstated
|